Before
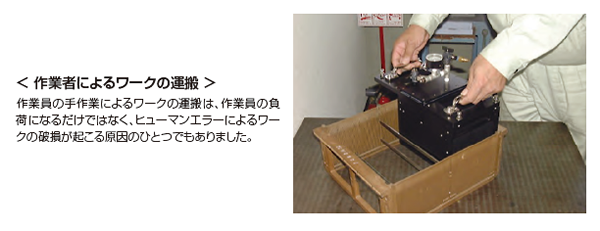
自動機の導入前までは、製造プロセスで作業員が張り付き、目視で工程を監視し、作業員が手作業で次工程にワークを送っていました。常時、作業員が張り付いていなかればならず、作業員が手作業で次工程へのワーク移送を行わなければならないため、作業員への負担もありました。また、ヒューマンエラーによるワークの破損トラブルが発生する可能性もありました。
コストダウン事例
After
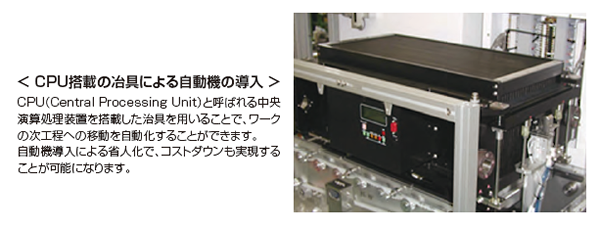
CPUを搭載した冶具を用いる自動化システムを導入することによって、プロセスデータを監視しながら、冶具単体が自動で次工程に移動することが可能になりました。これにより、常時作業員が目視にて監視する必要がなくなるため、人的工数の大幅な削減を達成することができました。また、手作業で次工程への移送がなくなるため、作業員の負担軽減にもつながりました。
自動機の導入前までは製造プロセスには作業員が常時張り付き、検査を行ったうえで次工程へ手作業にてワークを移動させていました。作業員の力量によって作業性が変わってくるので、生産リードタイムおよび品質が不安定でした。自動機の導入によって作業員数を減らし、コストダウンを実現するとともに、リードタイム、高品質な製品の供給が可能になります。