Before
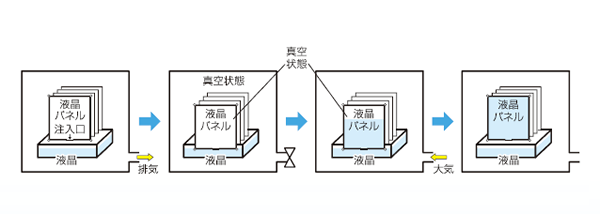
液晶をパネル間に注入する際に、従来は、セルギャップが維持できる条件を、真空状態から大気圧へ戻す圧力と時間をトライアンドエラーを繰り返しながら求めていました。トライアンドエラーには時間を要し、また、不良品が発生することもあるので歩留まりがよくありませんでした。さらに、精度にばらつきが出ることがあり、品質の安定が困難でした。
コストダウン事例
After
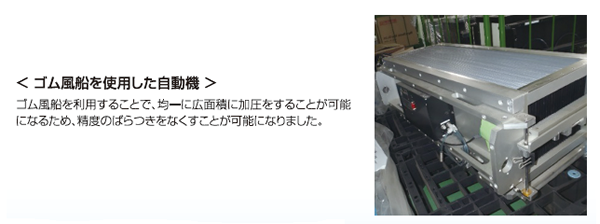
液晶注入後のパネルをゴム風船を用いて両面から加圧することで、広い面積を均一に加圧しセルギャップの調整が数値で行えるようになりました。これにより、安定した品質の液晶パネルを高い生産性を維持しながら作ることが可能になりました。また、液晶注入作業の管理が簡素化されることによって、液晶注入作業の作業性が向上しました。
自動機が導入される以前の液晶のパネル間への注入作業は高度な技術が必要であったため、作業者によって精度のばらつきが発生し、品質の安定が困難でした。また、適切な条件を求めるまでに時間を要し、生産リードタイムも長くなりがちでした。自動機の導入によって、液晶の注入作業が簡素化でき、品質も安定し、一気に生産性を向上することができました。