Before
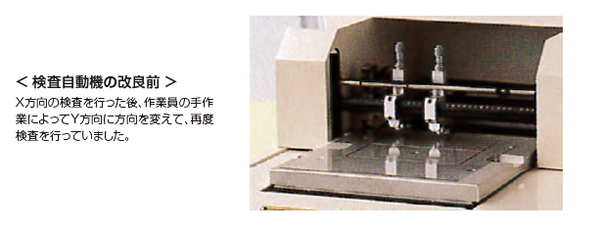
液晶などの微細な導線のショート・短絡の検査を行う際に、従来は一枚ずつ作業員が手作業で検査作業を行っていました。人手で行っていたためにワーク移動の際に、接触によりワークをぶつけ、ワークを破損させる場合がありました。また、検査の方向をX-Yで入れ替えを行う度に、一度停止し、ワークの方向の切り替えが必要であるため、検査のリードタイムも長くかかる要因となっていました。
コストダウン事例
After
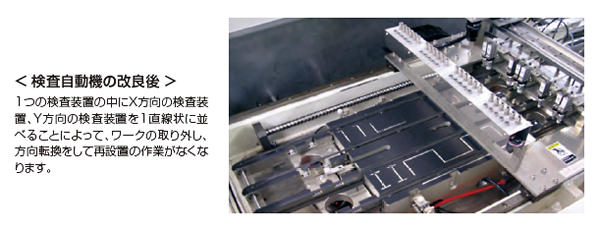
X-Yそれぞれの方向ごとの検査器を一直線に設置した自動機を導入することによって、ワークの方向を切り替える必要がなくなりました。ワークの取り付け、移動がなくなったことにより、人的ミスによるワークの破損を防ぐことができます。また、ワークの供給から排出までを含めて自動化にすることで、検査処理の時間短縮だけでなく、ワークの供給・排出時間も大幅に削減することができました。
検査工程において、ワークを自動供給する自動機が導入される以前は、全て手作業にてワークのセッティングを行い、都度、ワークの取り付け方向を変更していました。作業効率を最大限にできる配置とした自動機の導入によってリードタイムの短縮、品質の安定、人的ミスによるワーク破損の回避だけではなく、作業者の作業負担を軽減させることも実現しました。