Before
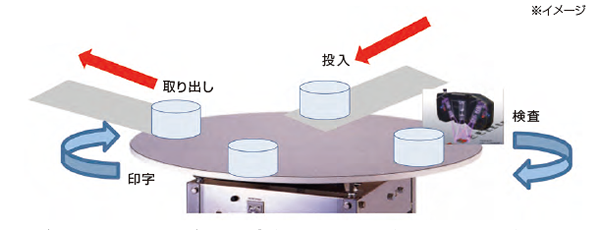
従来の自動機は1度のワークセッティングで複数の検査を行うために、ターンテーブル式の検査装置を用いていました。しかし、検査工程と印字工程における処理能力に限界がありました。また、何かのトラブルで自動機を停止した場合、検査工程も印字工程も停止してしまうため、生産工程が不安定になっていました。
コストダウン事例
After
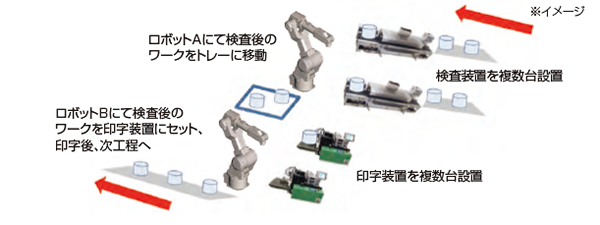
一直線に検査装置、印字装置を並べた生産ラインを導入することで、同時に複数個のワークへの検査作業、印字作業を行うことが可能になるので、生産性が向上しました。また、ロボットを導入することで、作業員がワークを移動させる必要もありません。また、ロボットを導入することによって省人化、無人化にもつなげることができ、トータルの製造コスト圧縮も実現することができました。
ターンテーブルの自動機を導入することによって、従来は個別の工程にて行っていたワークの投入から検査、印字、取り出しまでの生産性が向上しました。しかし、1度に流すことのできる量に限界がありました。そこで検査機および印字装置を一直線に複数台並べることによって、同時に検査、印字の工程を行い、生産リードタイムを大幅に短縮することに成功しました。